FLAXWOOD® IS A NATURAL ARCHITECTURAL TILE DERIVED FROM LINSEED OIL, DEVELOPED IN COLLABORATION WITH THE DUTCH DESIGNER CHRISTIEN MEINDERTSMA.
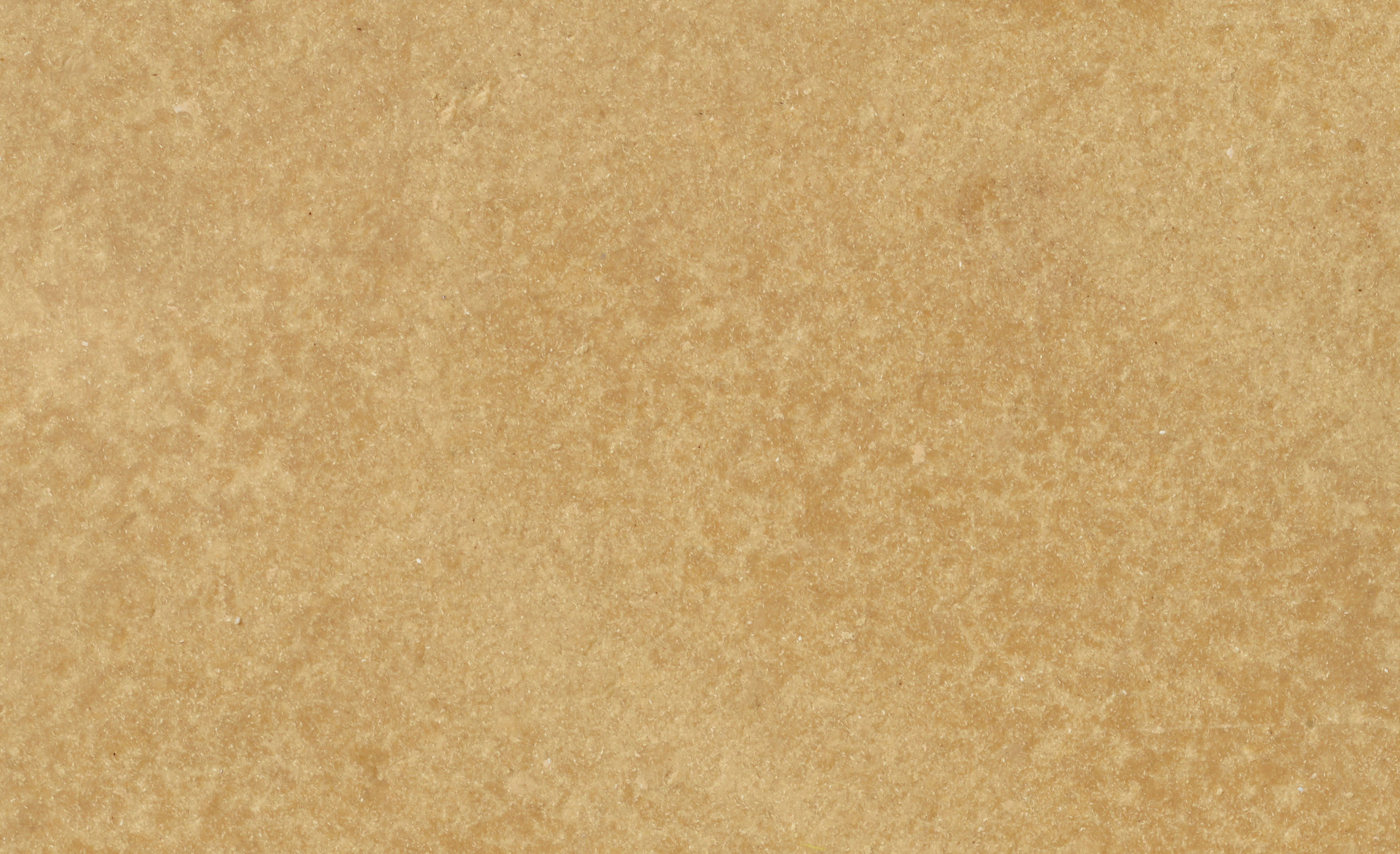
Flaxwood® disrupts the traditional linoleum production mid-process in order to create a more natural, three-dimensional expression of an inherently renewable, biodegradable material. Our ambition is to offer a fully renewable, fully traceable architectural product.
We debuted an 8mm thick, solid-through, tile during Milan Design Week 2024. Flaxwood® is now in an optimisation and testing phase and we hope to offer it commercially by the fourth quarter of 2024.
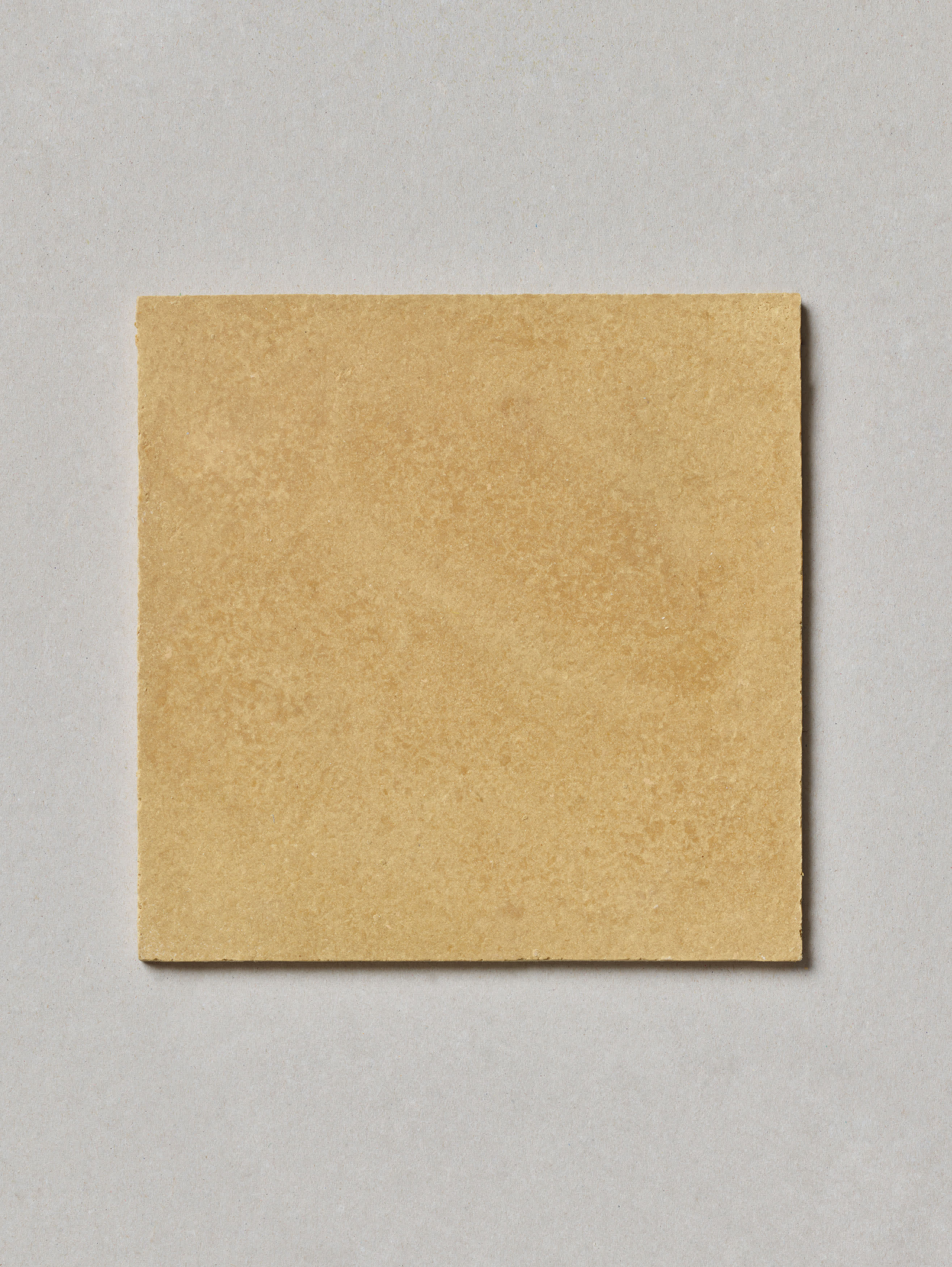
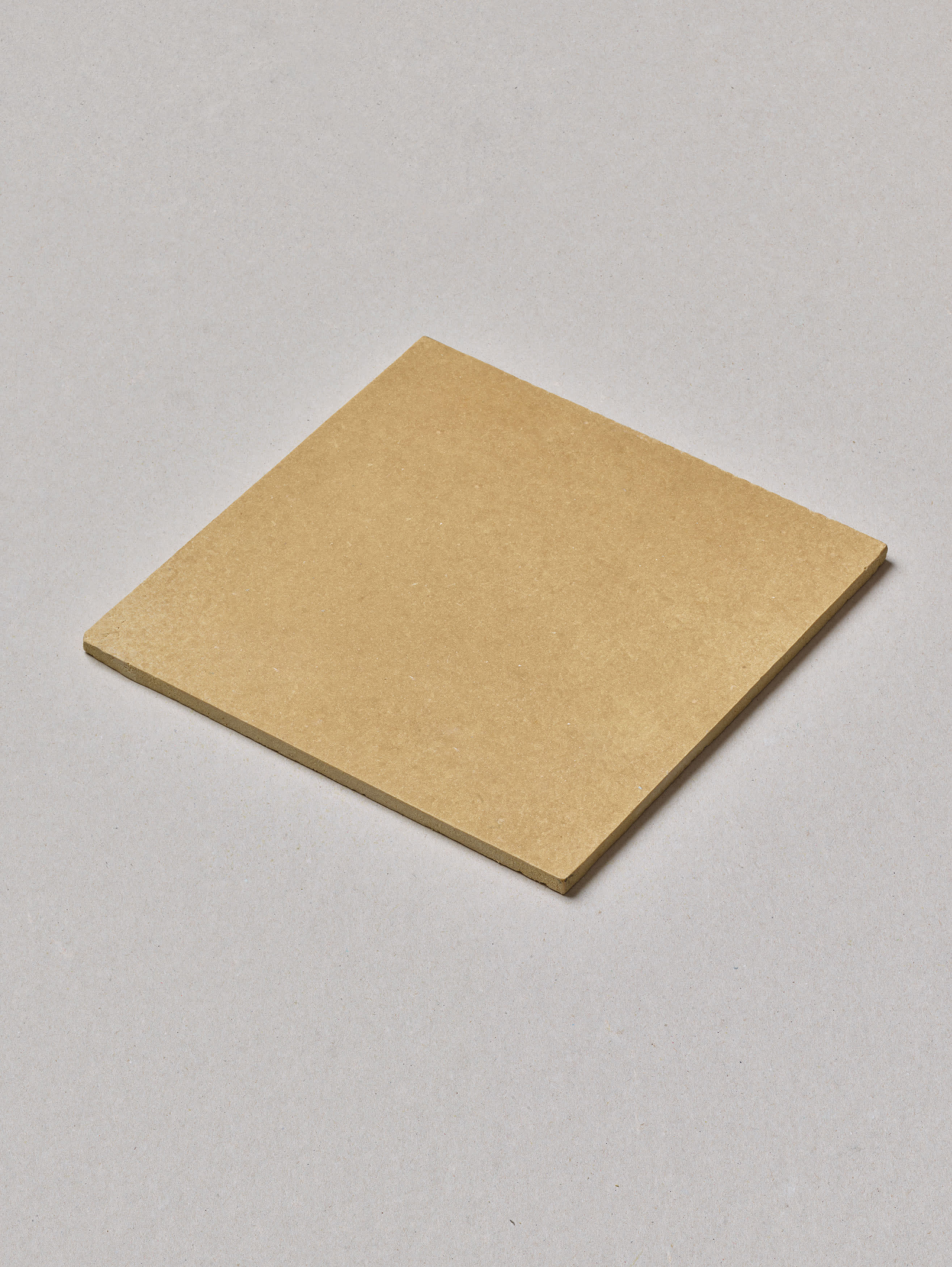
STORY
The English inventor Frederick Walton pioneered linoleum in 1860, at a time when the Aesthetic Movement in Britain was beginning to take shape. The artists of the day were reacting to a perceived ugliness and materialism in the Industrial Age by championing beauty as the central tenet of their practice. William Morris was one of the movement’s most revered creators, and his elaborate, colourful patterns for wallpaper and tiles had an immeasurable impact on the visual principles of the period. Linoleum’s aesthetic values were defined in those early days and the material’s course hasn’t strayed too far from the strong colour and pattern that defined it.
Twenty-first century architectural materials have an environmental mandate that their nineteenth-century predecessors did not. A tangible design emergency calls on us to reconsider every part of the built environment in order to reduce the human impact on climate. Mass-produced modern day linoleum stands as a testament to sustainable material innovation, comprised of 98 per cent natural raw materials, 71 per cent of which are rapidly renewable or recycled. In spite of these admirable metrics, linoleum continues to be shockingly overlooked in favour of its cheap, petroleum-based imitator, vinyl. This is partly down to the two materials being commonly misunderstood as analogues. Linoleum’s stewards have frustratingly sought to mimic materials such as marble, granite, wood or even concrete, never content to allow it to be its own thing.
Flaxwood® retools a 19th-century innovation, moving away from synthetic aesthetics in order to present a more honest material language that can properly respond to this moment.
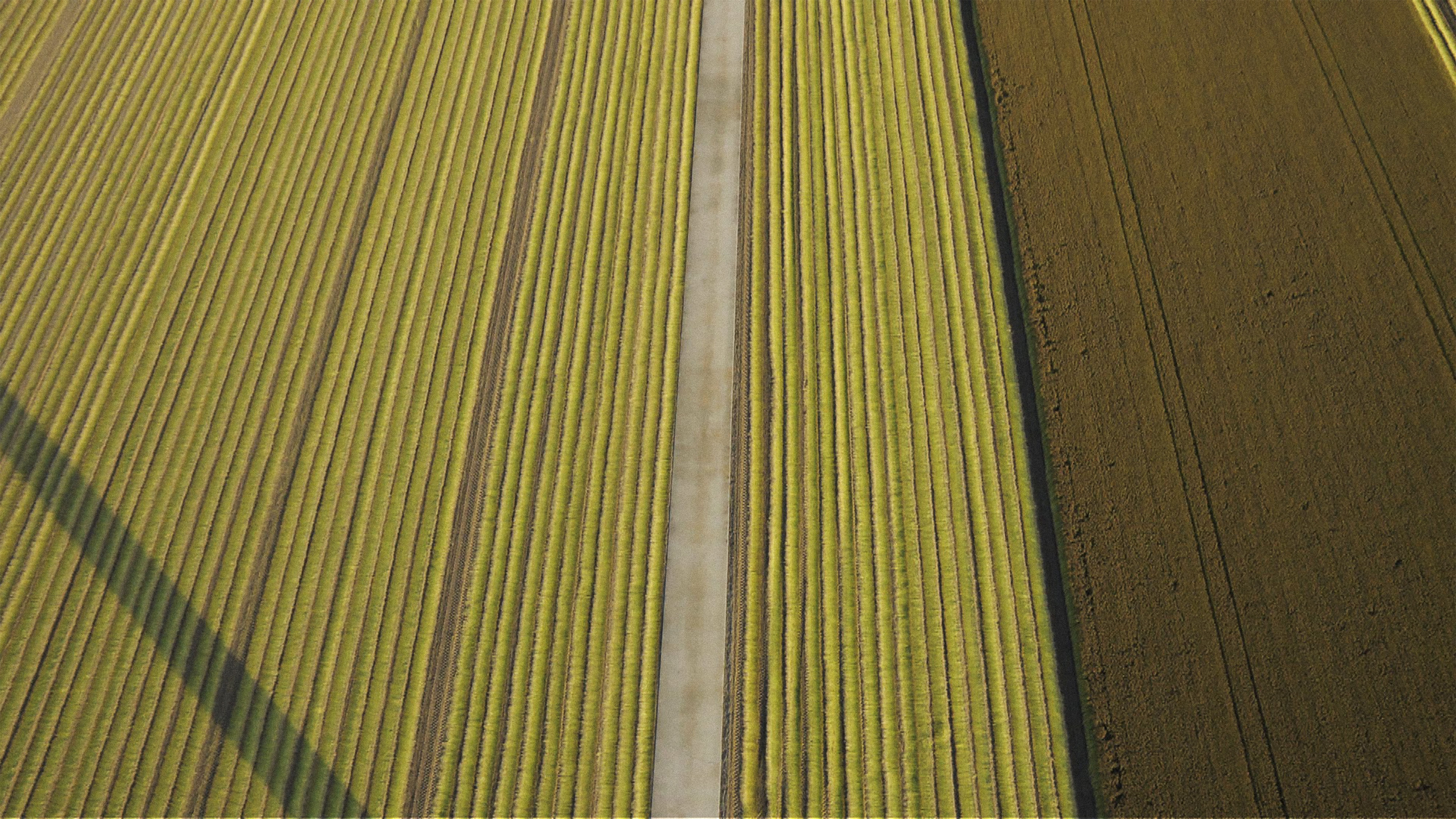
Plot Gz59-west in the Dutch Flevopolder of Flax farmer Gert-Jan van Dongen.
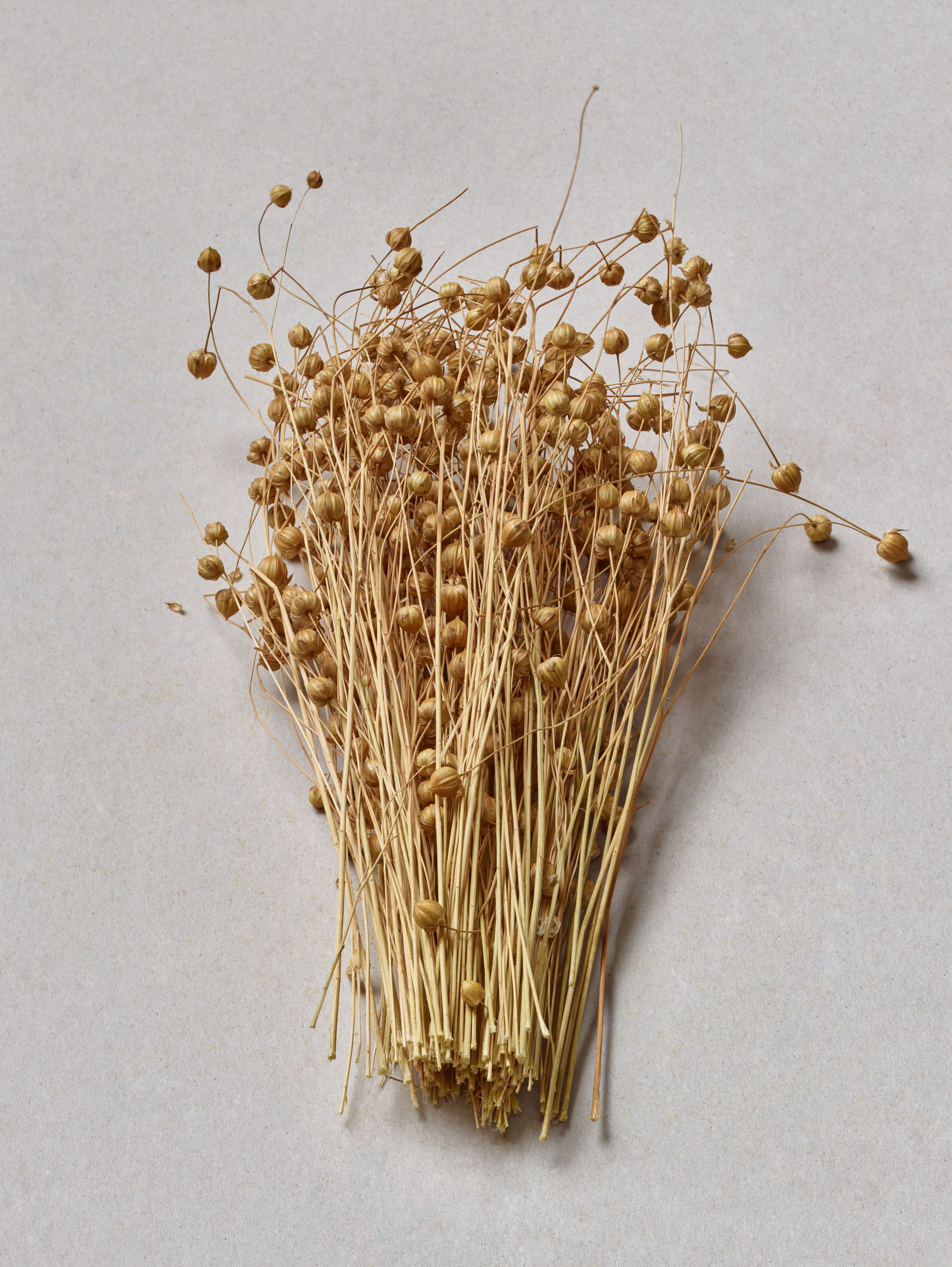
The linseed oil used in our production comes from pressed flax seeds from the flax plant.
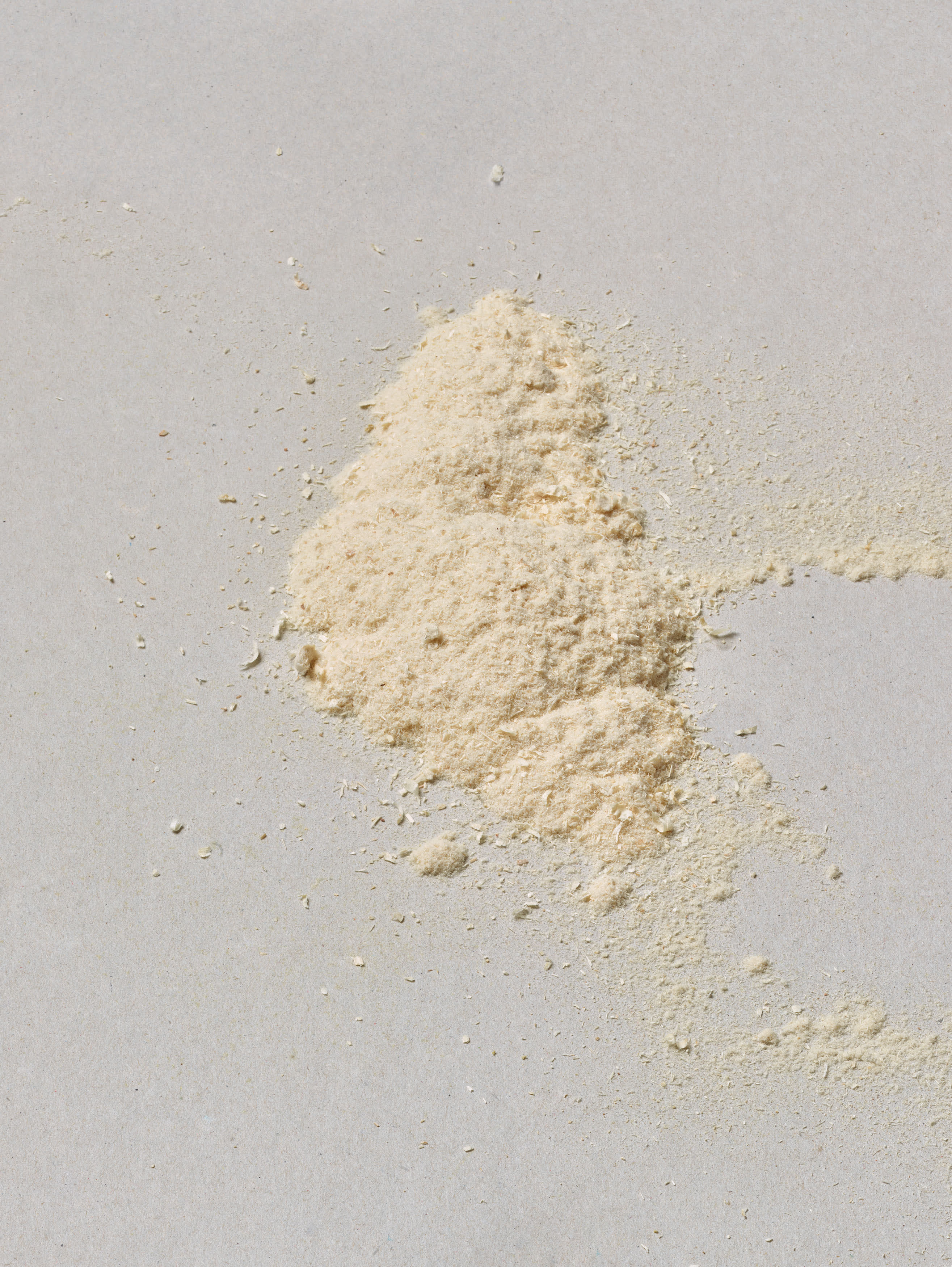
Wood dust
"BY RECONSIDERING HISTORICAL PRODUCTION METHODS, WE CAN IMAGINE NEW VOCABULARIES AND FUTURES FOR A MATERIAL." -Christien Meindertsma
Flax has been central to Christien’s practice over the past 16 years. In 2012, she purchased the entire harvest of a Dutch flax farmer with the aim of recreating a once-thriving local ecosystem from flax farm to finished product. Her Flax Project is ongoing, with explorations ranging from traditional yarn spinning and rope construction to high-tech textile composites so robust that she has used them to make an entire chair. Linoleum, as a flax-derived product, was naturally of interest to her.
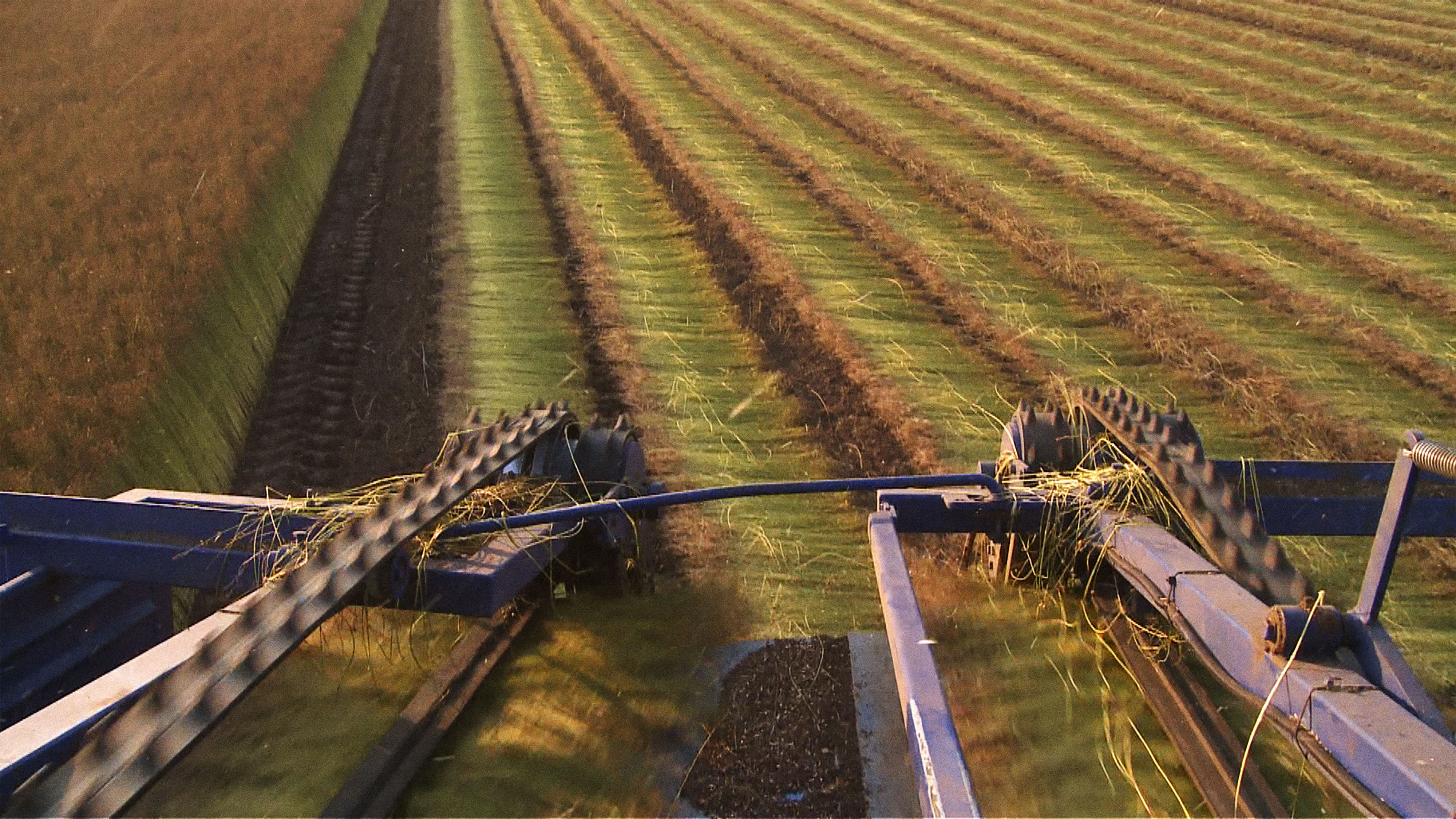
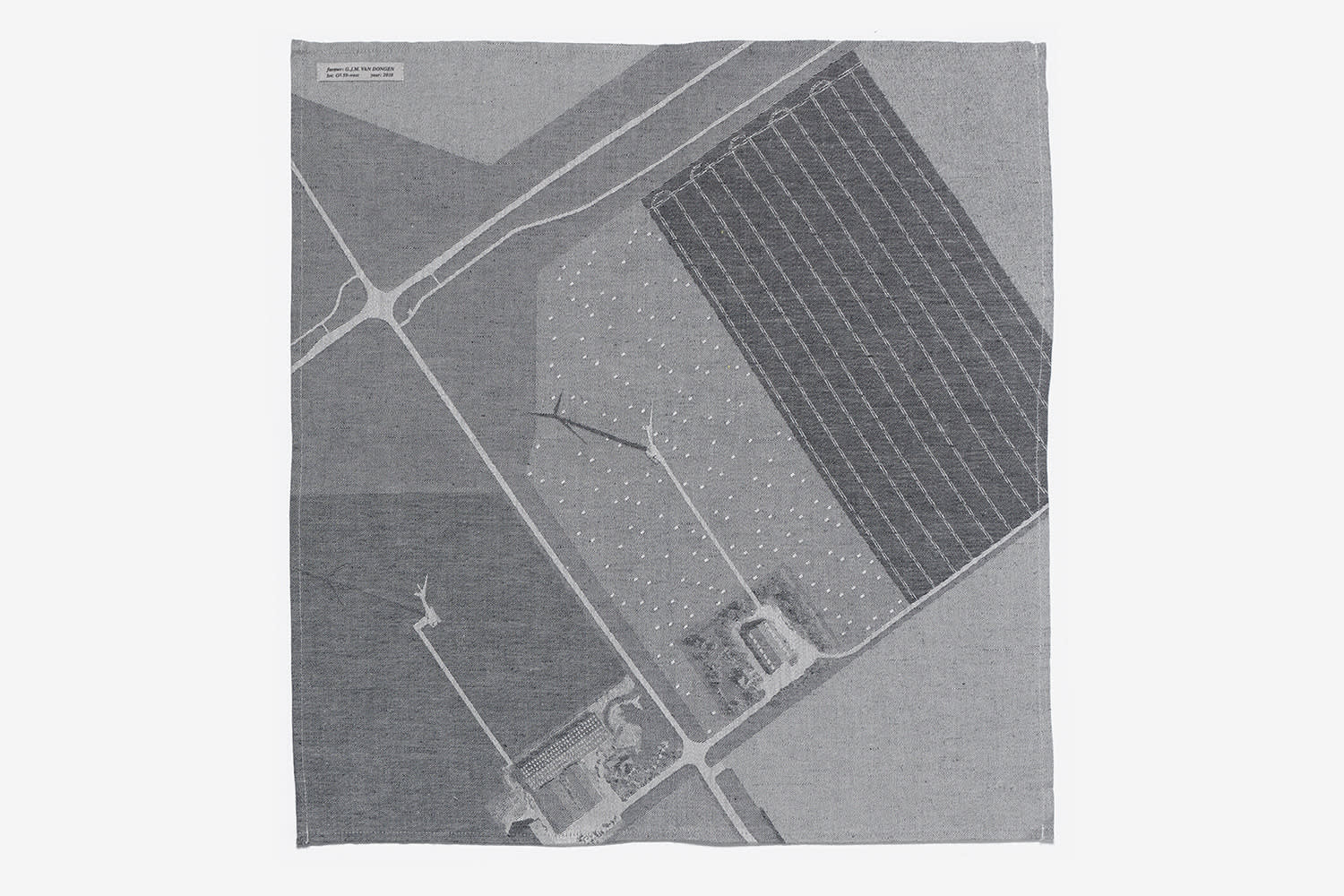
Topographical Damast table linens made from the 2012 harvest of Gert-Jan van Dongen. Produced by Thomas Eyck in 2016. Image Mathijs Labadie
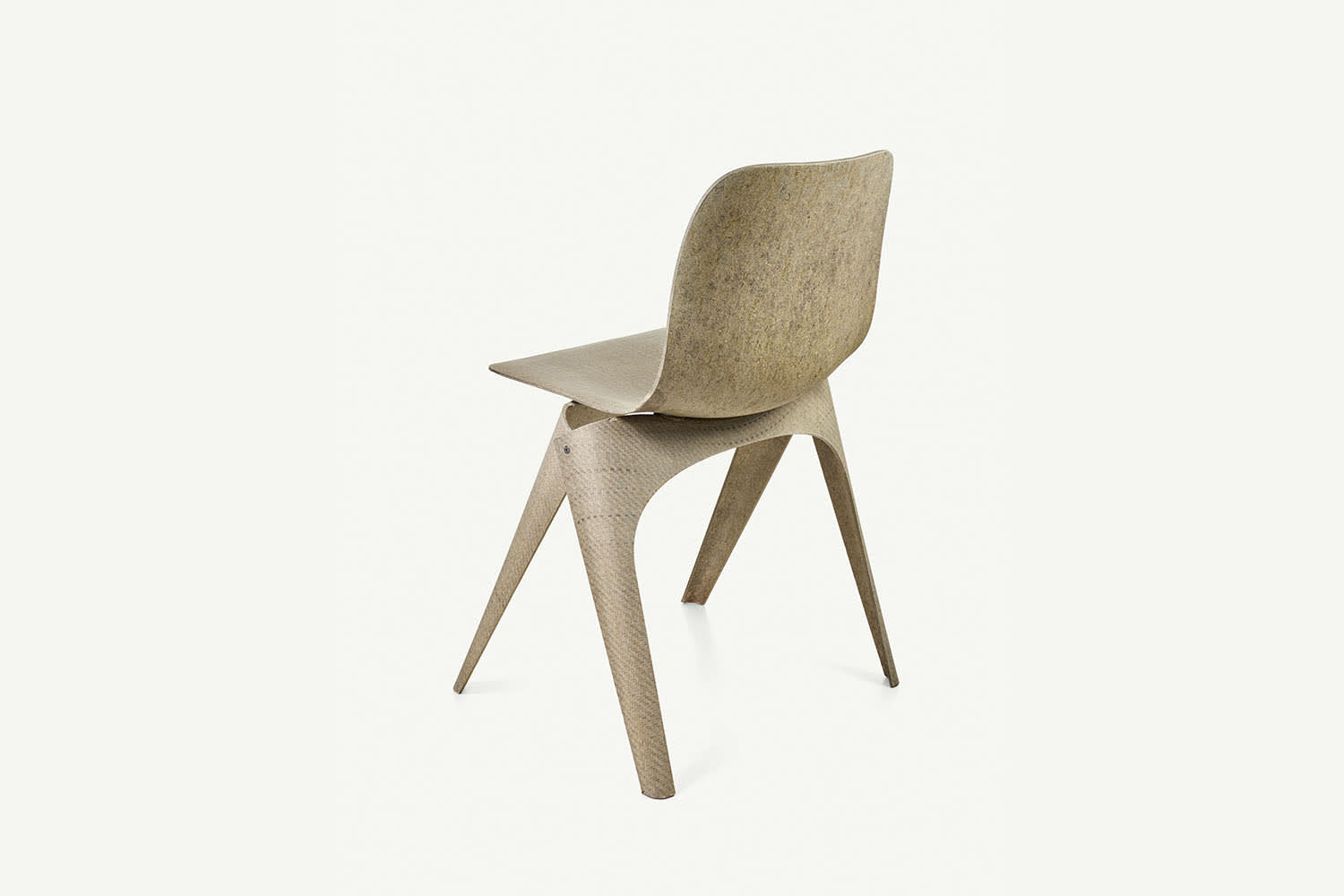
Initiated by Label/Breed, Meindertsma collaborated with natural fibre specialist Enkev to develop a new four layer composite of woven and dry-needle felted flax that could be made into rigid products such as this Flax Chair, 2015.
Christien has extensively researched the linoleum system, from material supply chains to production methodologies.
Renoleum (2019) explored the potential of re-using old linoleum floors in the production of new linoleum. No Peat Lino (2022, Fries Museum commission) replaces wood dust with cattail and reed stalks from the Frisian peatlands. Local Linoleum (2023, V&A Museum commission) proposes to make a solid and local linoleum from wood- processing wastes that is also re-pliable at its end of life.
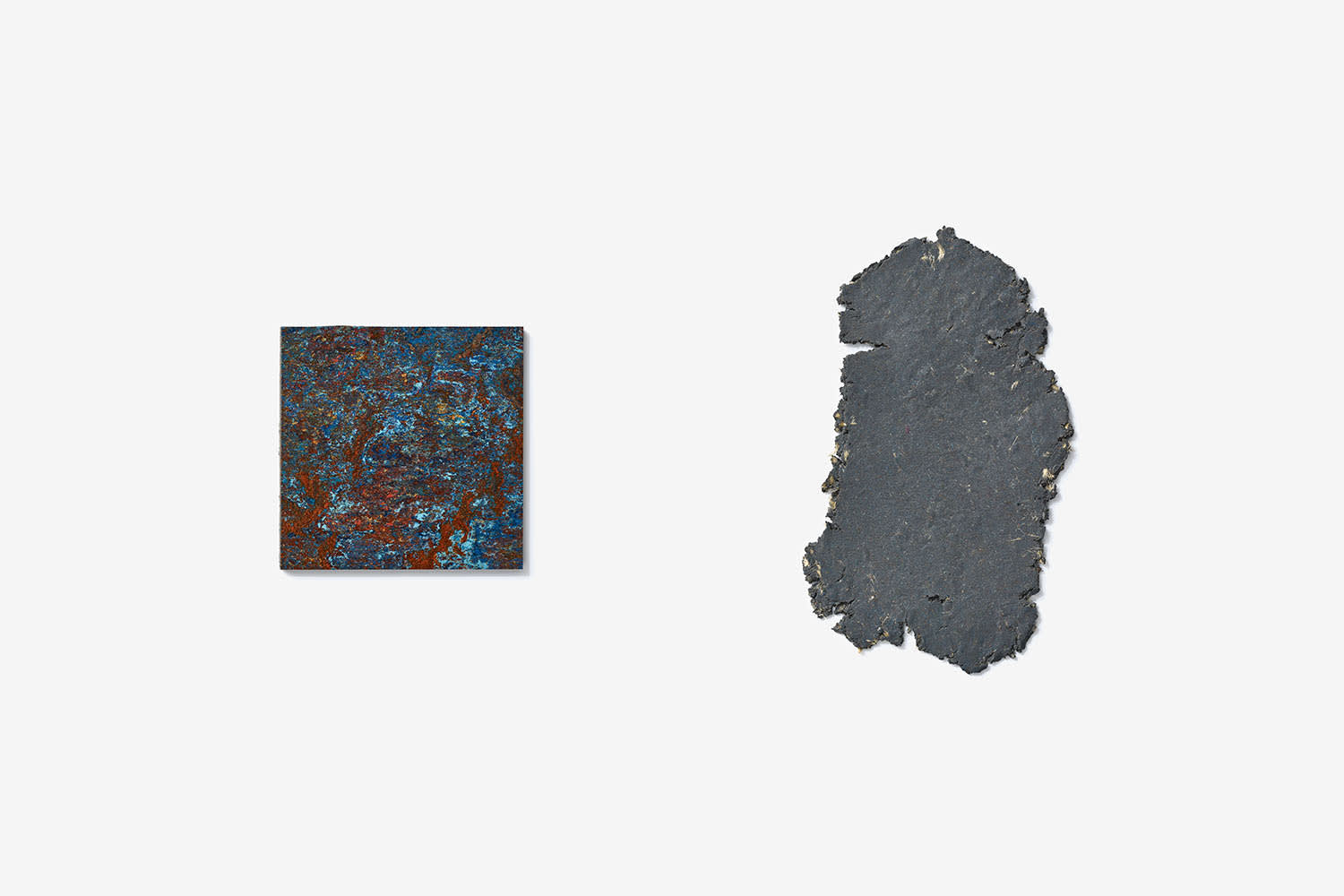
Research from Christien's Renoleum project which explores the elasticity of old linoleum.
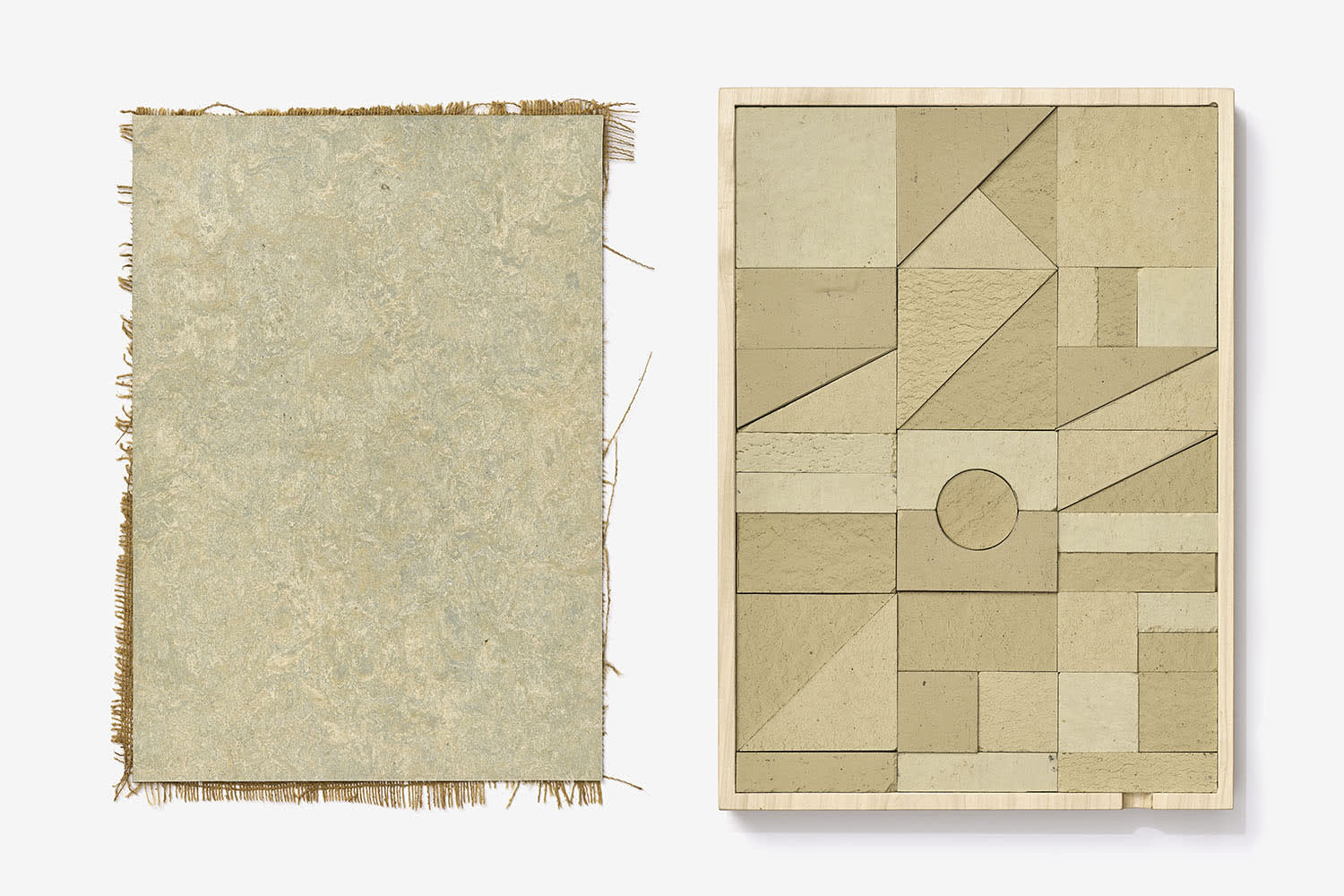
Christien was inspired by the Classic Anchor Block sets.
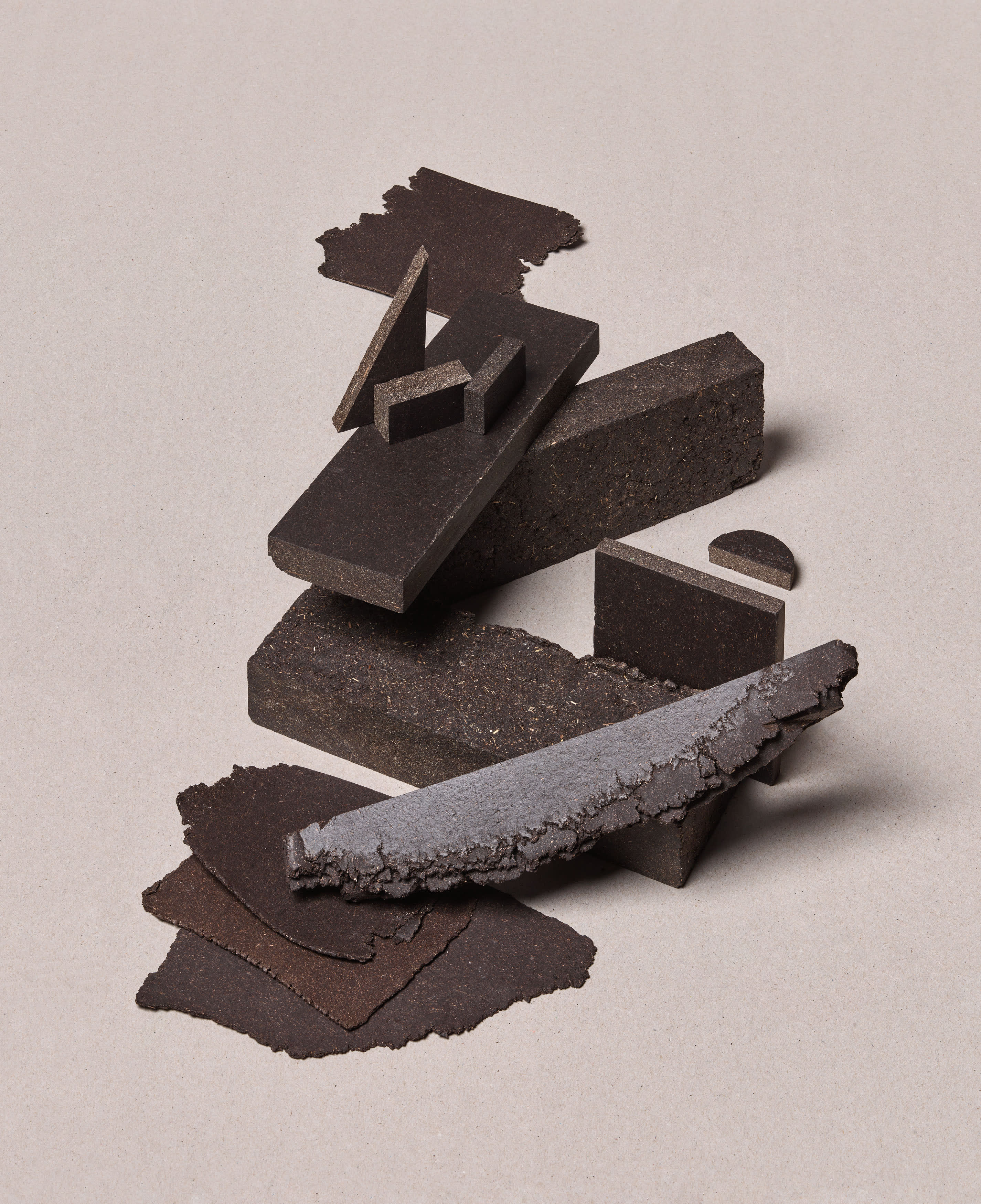
These 'No Peat Lino' experiments form part of a 2022 commission from the Fries Museum, NL that has culminated in the Fertile Grounds exhibition. These tests replace wood dust with fast growth reed, willow and cattail available in the Frisian peatlands.
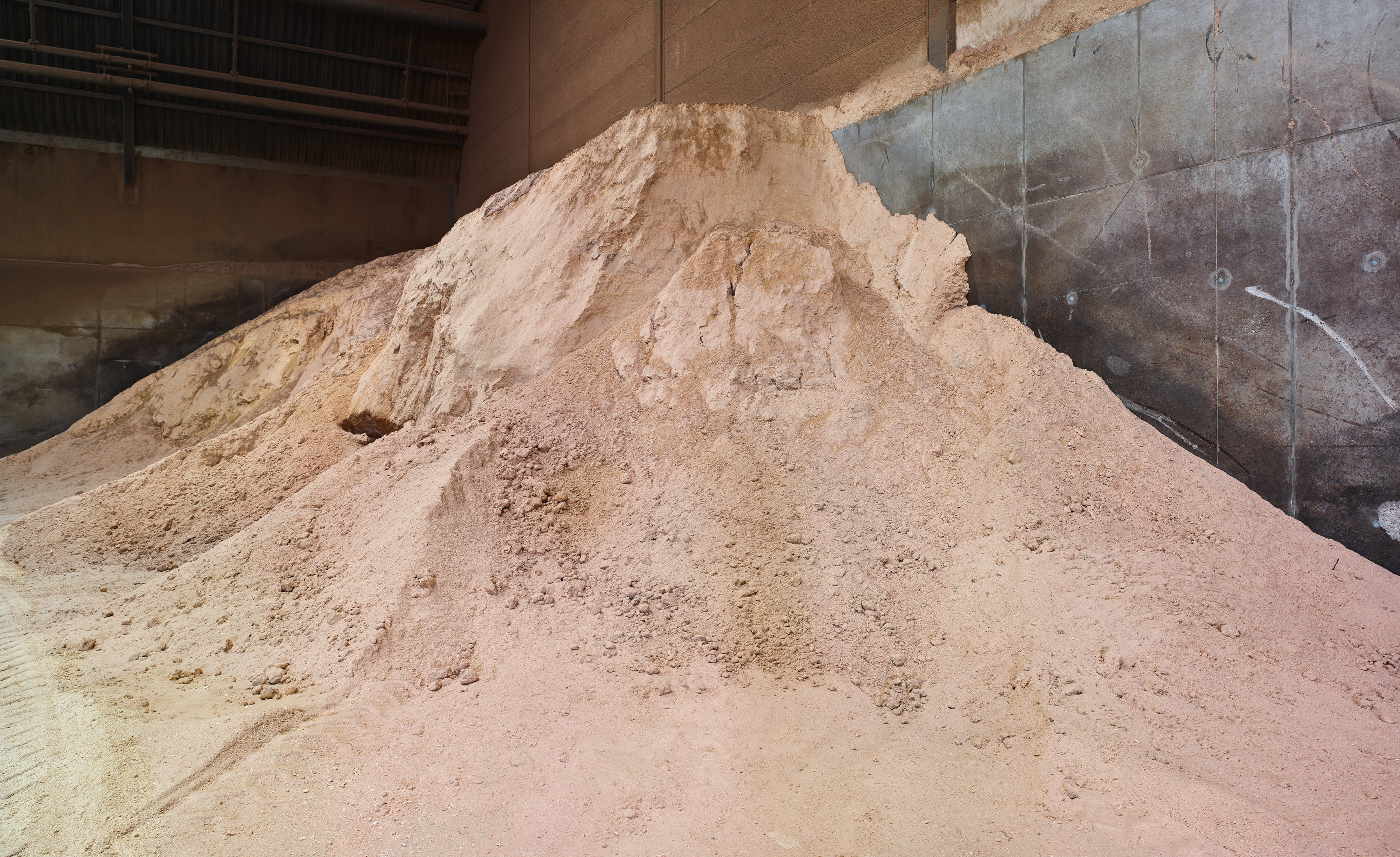
Wood dust piles from a local Dutch woodworking company.
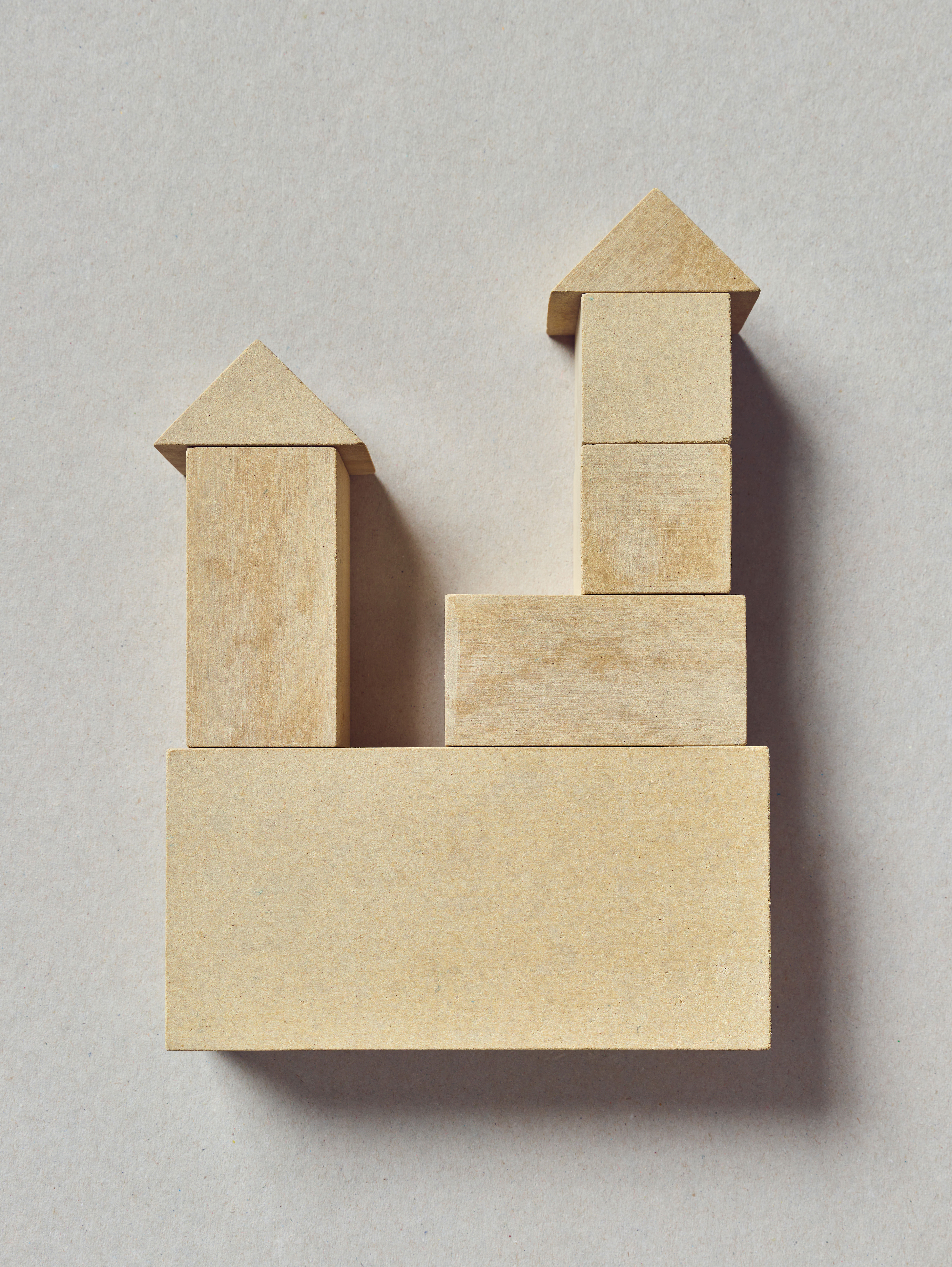
Commissioned in 2023 by the Victoria & Albert Museum, UK, as part of their Make Good, Rethinking Material Futures Programme. These experiments use wood dusts that are a byproduct from local furniture industry and woodworking companies.
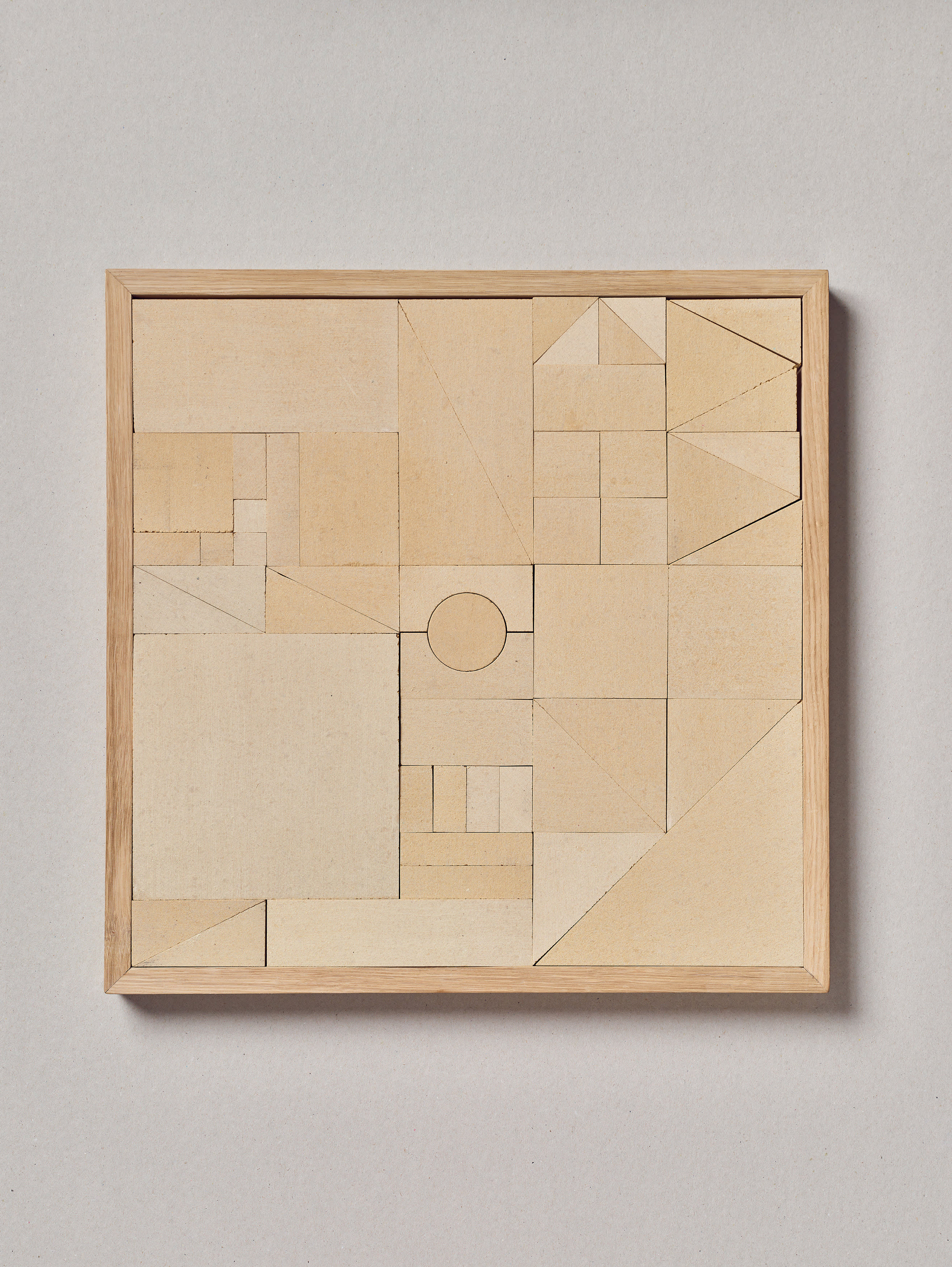
Local linoleum block set made as part of the V&A commission.
PROCESS
Roel van Tour's film depicts the 2012 flax harvest of Gert-Jan van Dongen and the process of converting part of that crop into a linseed oil from which we can then produce Flaxwood.
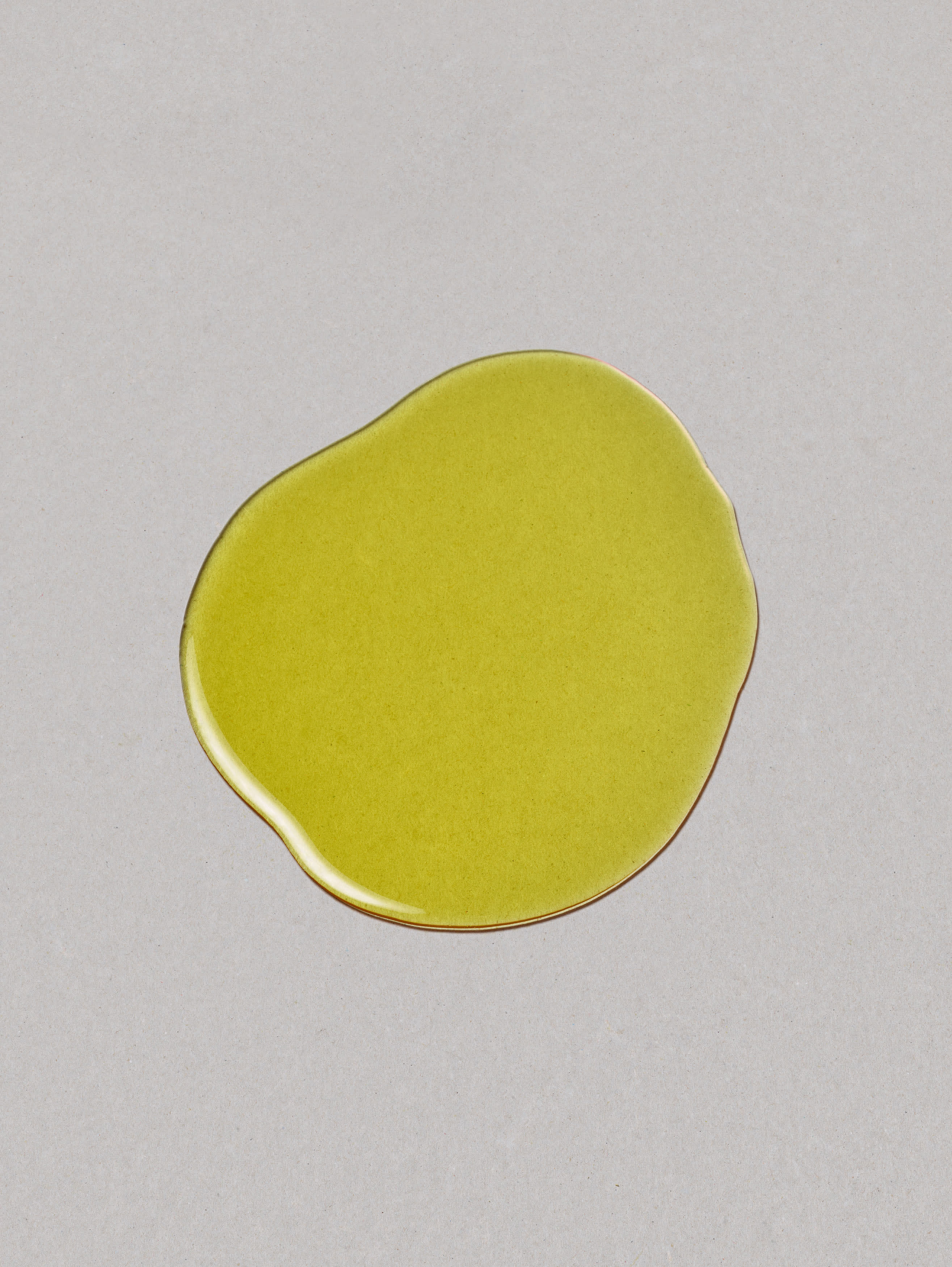
Linseed oil
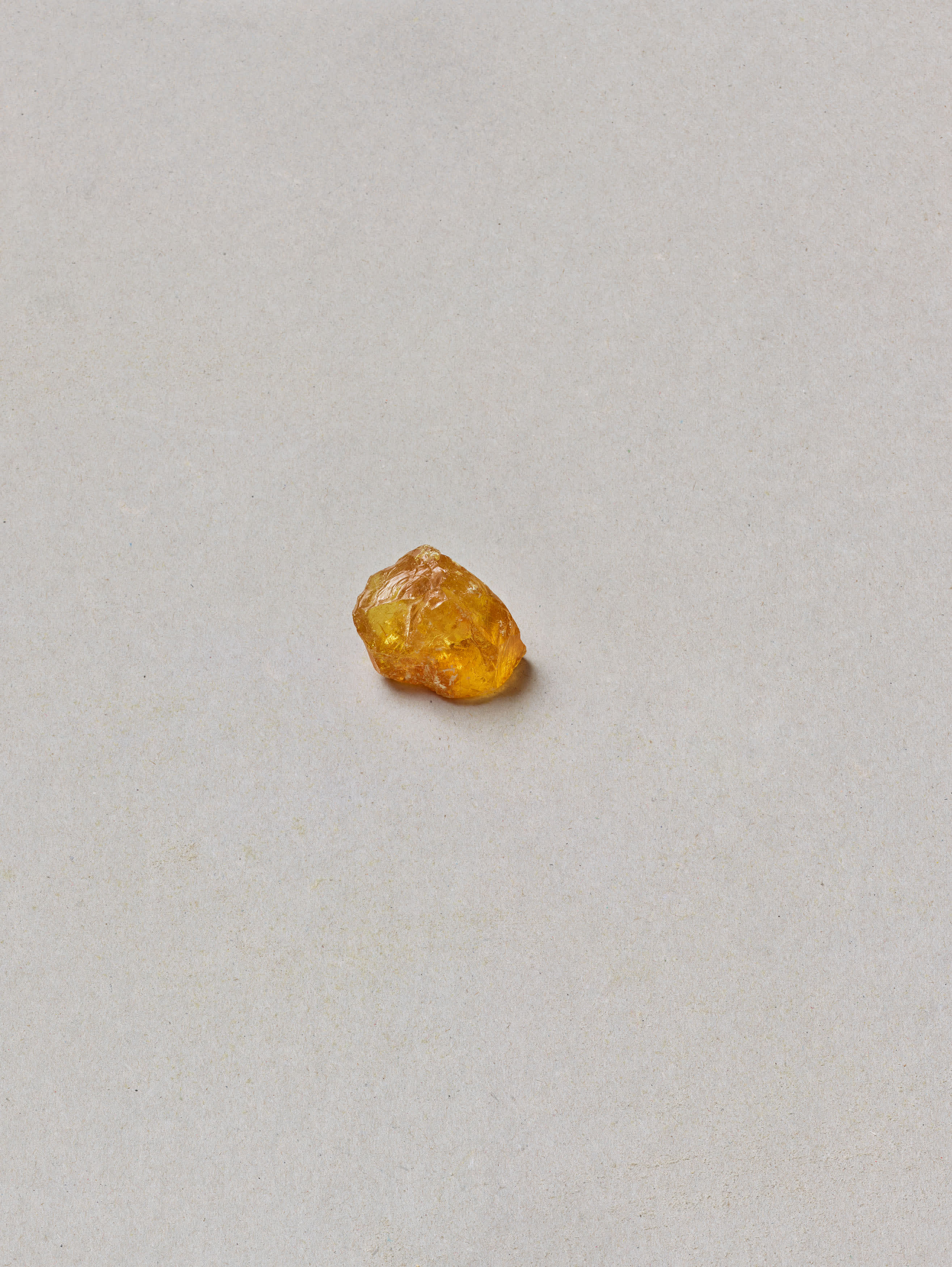
Pine Rosin
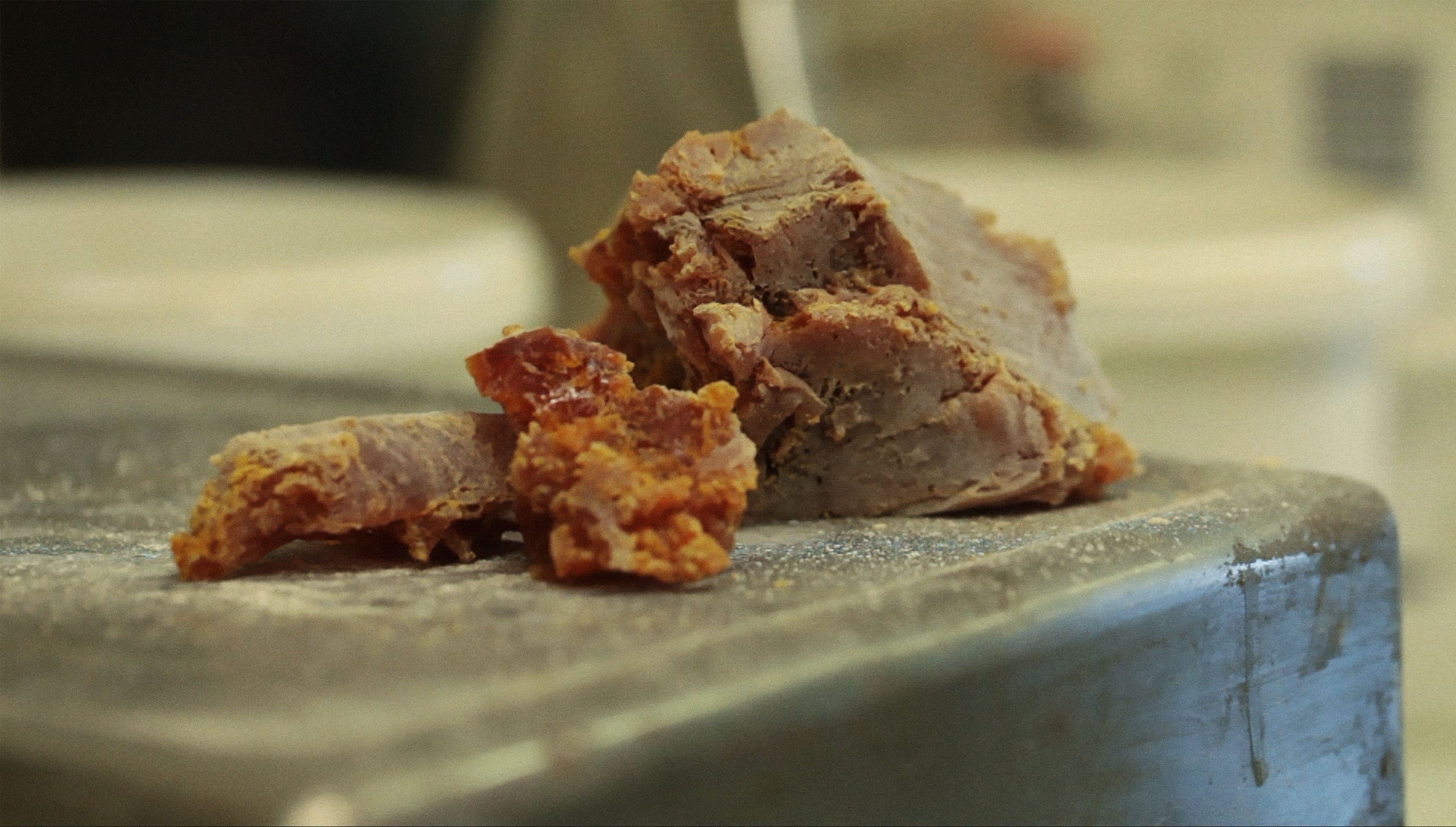
Flaxwood dough is a combination of boiled linseed oil and pine rosin
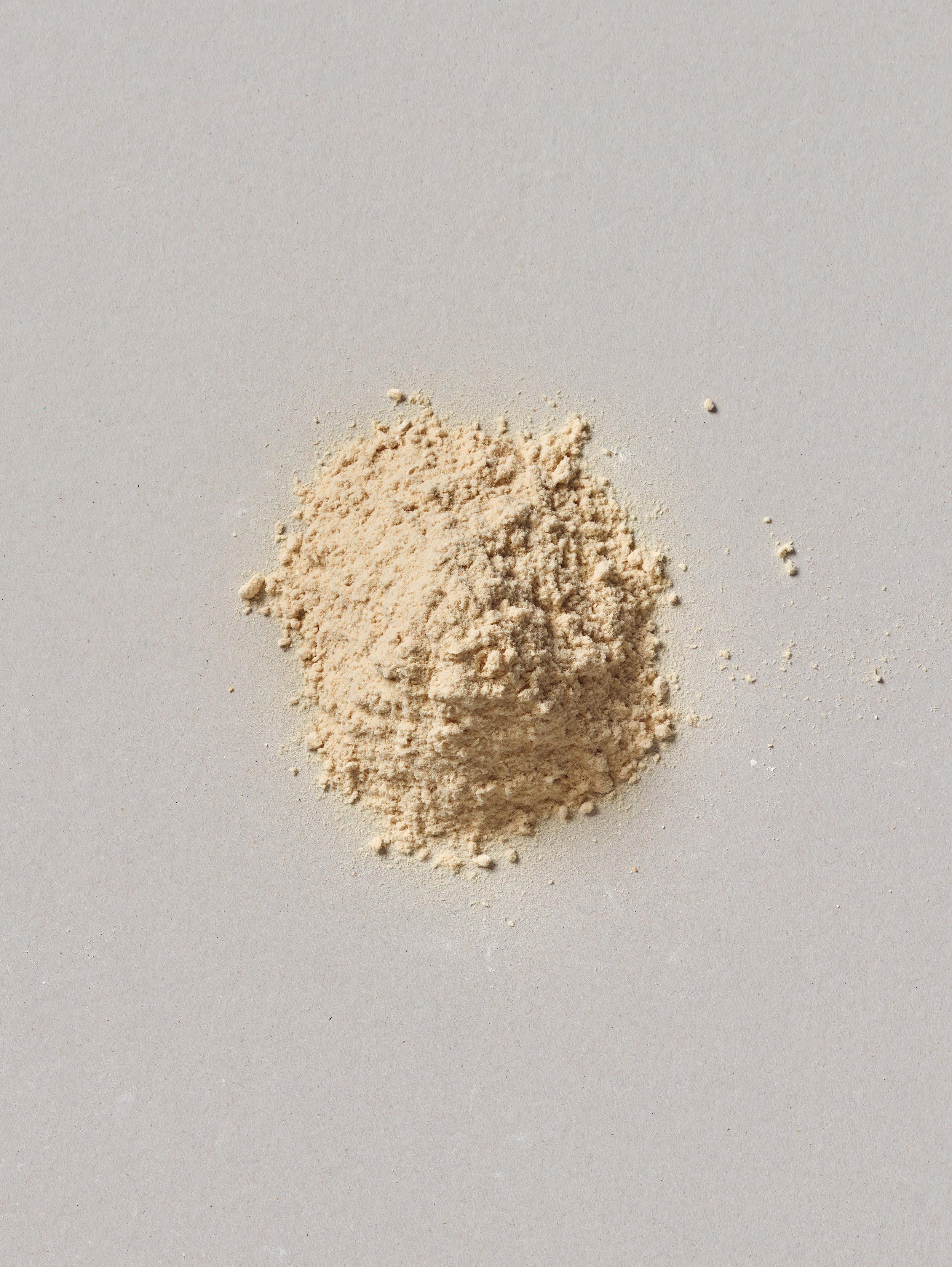
Wood dust used in the production of Flaxwood
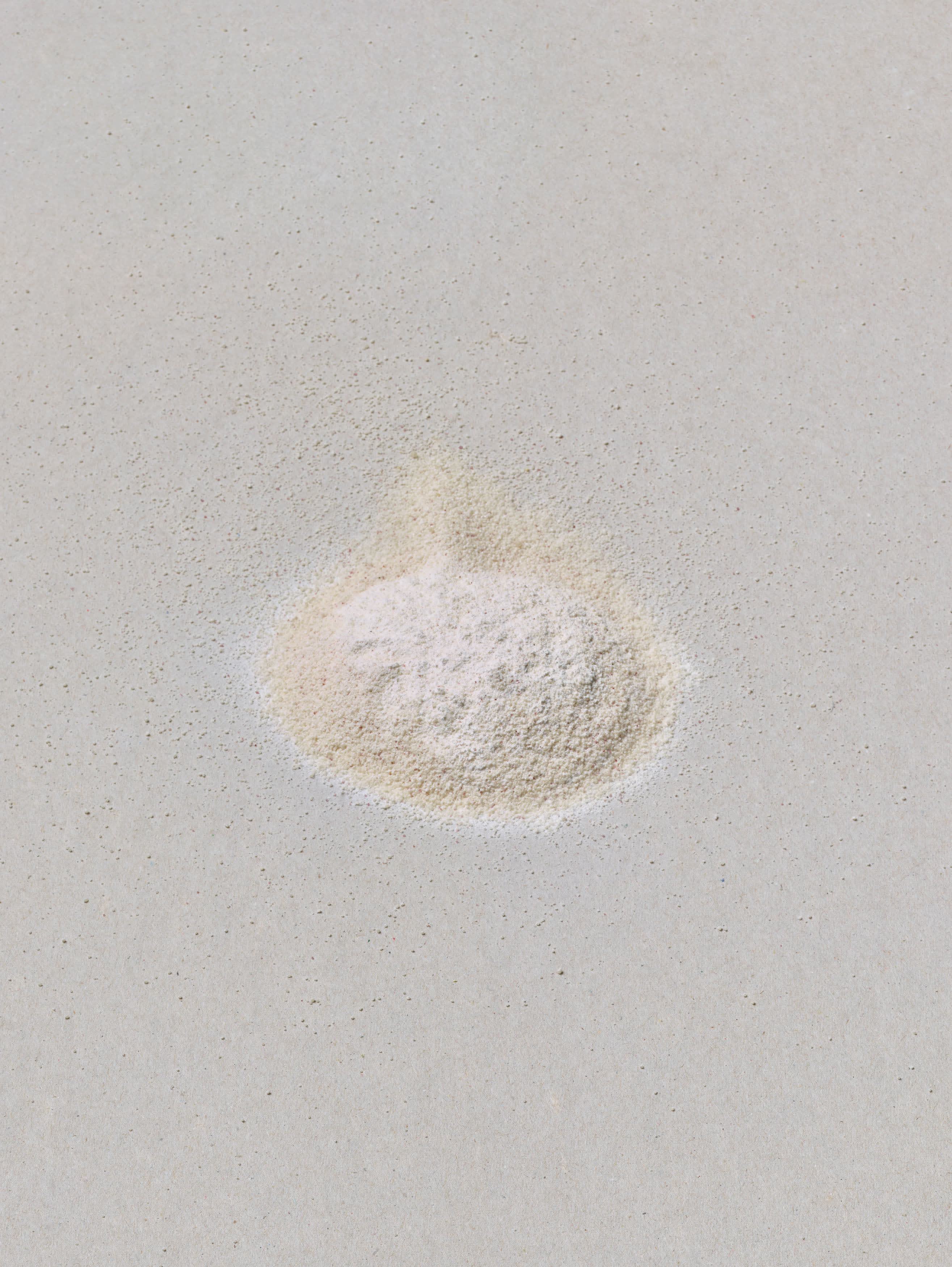
Calcium carbonate
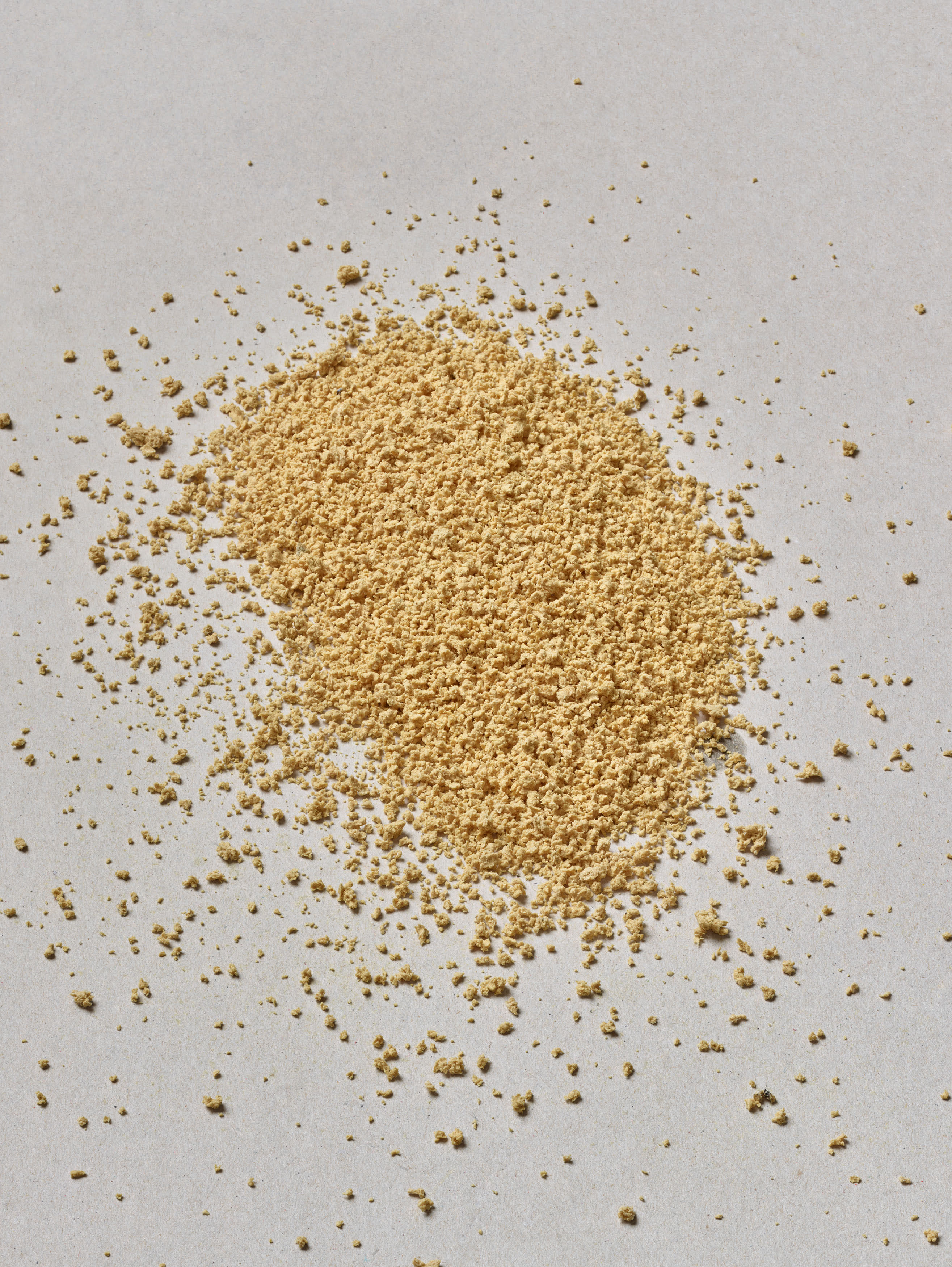
Combining all the ingredients and chipping them into a granulate which we then press to shape